Summary: 1.Durability comparison: Aluminum-magnesium-manganese alloy can form aluminum oxide film with the atmosphere to prevent ...
1.Durability comparison: Aluminum-magnesium-manganese alloy can form aluminum oxide film with the atmosphere to prevent further corrosion. It is generally used for civil buildings with a 15-20 year warranty on coatings. The design life of the building is more than 50 years. Generally guarantee the product warranty period of 25 years; color steel plate is easy to corrode and rust and cause fracture accidents under the erosion of humid air and rain and snow water, especially the parts of rivets and joints.
2. Weight comparison: Light weight of aluminum-magnesium-manganese alloy (density of 2730kg / m3); heavy weight of color steel plate (density of 7850kg / m3)
3. Contrast of strength and rigidity: The aluminum alloy of aluminum-magnesium-manganese alloy contains magnesium and manganese, so it has certain strength and stiffness. However, the internal stress, hardening, and strength of aluminum alloy plates have no obvious yield points, which is not as good as that of color steel; the strength and stiffness of color steel plates are better. Not easily deformed.
4.Appearance control: aluminum-magnesium-manganese alloys can be divided into non-painting (hammer, embossing, pre-passivated alumina surface treatment, etc.) and painting (pvdf, smp, pe, etc.); color steel plates can be divided into Unpainted (hot-dip galvanized steel strip: smooth plate) and painted (pvdf, smp, pe, hdp, etc.).
5. Lightning protection performance: The thickness of the aluminum-magnesium-manganese alloy is generally 0.7mm and 0.9mm, which can be directly used as a lightning arrester (National Standard << Building Lightning Protection Design Code >> gb50057) to avoid perforation on the roof; color steel plates are generally Use 0.5mm thick aluminized zinc and galvanized steel plate, can not be used as lightning arrester, you need to set up a lightning arrester (such as a lightning rod).
6. Safety and fire protection: Al-Mg-Mn alloy has a low melting point (660 degrees Celsius). The high temperature resistance is poor, and the strength is rapidly lost above 150 degrees. When a fire occurs, the roof is easy to be burned through, which makes the fire spread outwards instead of inwardly and horizontally, which helps firefighters to extend the fire hose from the top; the color plate steel has a high melting point (1515 degrees Celsius).
7. Forming: Al-Mg-Mn alloy has good weldability, high plasticity, under low temperature environment, the strength and ductility of aluminum alloy are improved, and it has good low-temperature workability; color steel plate is prone to cold brittleness at low temperature .
8, cost-effective: aluminum-magnesium-manganese alloy is more cost-effective: light weight, waterproof, easy to bend arc, good stereo vision effect; color steel plate is less cost-effective: heavy weight, slightly poor waterproof, rigid strong curved arc, artistic effect Not good.
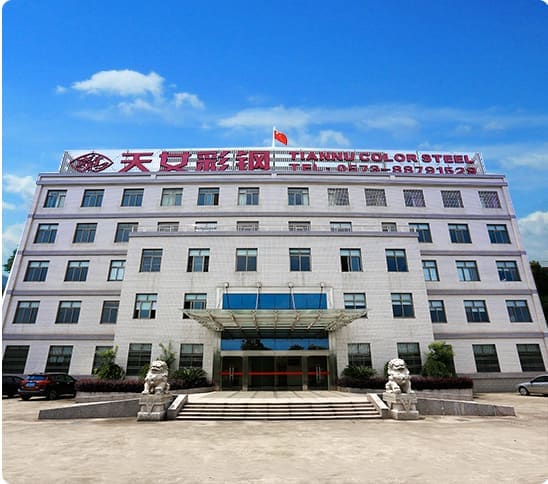